Brass is an alloy consisting of copper (Cu) and Zinc (Zn) and exists in two general categories:
Red Brass: The two main constituents are Zn at less than 15wt % Cu at greater than 80wt %. This alloy has a red tint because all the Zn is dissolved in the Cu. This material rarely shows dezincification, but little difficult to machine.
Yellow Brass: The two main constituents are Zn at more than 25wt % Cu at less than 60wt %. This alloy has a yellow tint because the Zn forms its own separate regions in the alloy. This material is cheaper and easier to machine than red brass. A good visual picture is to imagine this brass to be a chocolate chip cookie. The chips would represent the Zn rich phase. The rest of the cookie is the copper rich phase. Machining of yellow brass is improved by adding lead (Pb). During machining, the lead acts as a lubricant and causes the chips created by the cutting to break off easier.
Dezincification of Brass
Dezincification is the corrosion of an alloy (i.e. metal) where the Zn in the alloy reacts preferentially in a corrosive environment. Basically it is a process in which zinc is lost and copper is left behind. Red brass (i.e. <15 wt% Zn) rarely suffers this type of corrosion because the Zn is still in the Cu matrix. Yellow brass with >25wt% Zn is susceptible to dezincification. This is because there are Zn rich regions in the alloy. The less noble metal, Zn, is removed from the alloy by galvanic corrosion on a microscopic-scale. The most susceptible alloys are the ones containing regions of metals with high difference in the galvanic series, e.g. copper (much more noble) and zinc (more reactive) in brass.
A schematic of galvanic corrosion is given in Figure #1. There are two effects of dezincification on a brass alloy. The Zn rich regions are eliminated and a white zinc oxide (called a meringue) is formed on the fitting interior (see Figure #2). This meringue can plug fittings and restrict water flow (See Figure #3). In addition, the brass becomes porous (See Figure 4). The porosity weakens the brass and also may cause leaking.
Metal suppliers are developing yellow brass alloys to decrease the occurrence of dezincification. There are many factors that contribute to dezincification; these include water chemistry, temperature, flow and pH. For this reason, it is hard to predict how well an alloy will perform in any situation. For this reason, dezincification resistant alloys have been developed; however, their performance is not guaranteed. These fittings are marked DZR; this means dezincification resistant (see Figure #5).
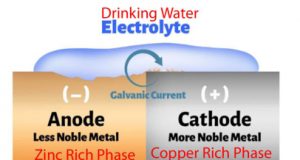
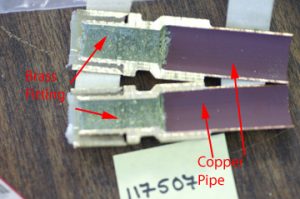
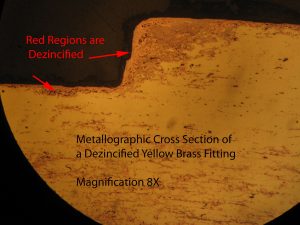
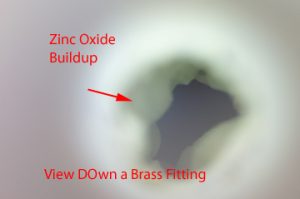
i went to a house to look at a water leak at the hot water heater.
The fittings entering the heater were leaking on the top of the tank entrance. When I tried to re-crimp the PEX ring to stop the leak the fitting snapped off. A PEX elbow about 4 feet above the tank showed some blue oxide indicating a possible minor leak. I was going to try to re-crimp this fitting but the elbow broke when I moved it. The fittings were deterioted and very brittle. I was going to re-plumb from the tank up to the other fittings when the cold water connection at the tank also broke off. Same brittle problem and thin metal. These fittings all have blue oxide on them. Any help and suggestions is needed. Thank you
I recommend changing the fittings. Hopefully you can find red brass fittings. I would need to know more before responding to the blue oxide.
I replaced all fittings available in un-finished basement with plastic.
All replaced fittings were badly croaded and had blue oxide on them. I did not replace fittings in the walls and do not their condition
Am not aware of red brass fittings. Would”t plastic be better?
I had water tested thinking high iron, but came back just a little high.
I was told that zinc in brass fittings is susstible to this corrsion
Plastic could work if they are high quality
My house built in 2011 has the Zurn brass fittings Qpex and uponoor pex pipes. The fittings are all corroding but not leaking yet. Plumber says it is dezincification and the only solution is to replace all the fittings. Is there any other solution? Does a water conditioner using salt make it better or worse?
Hello Dean,
The best solution i sto replace the fittings with red brass fittings.
Tom, I am looking at a commercial project where brass fittings were used with PEX piping for domestic water, and the fittings are suffering from likely dezincification. The engineer’s specifications required the use of fittings meeting ASTM F877 or ASTM F1807, ASTM F1281, or ASTM F1986. Do you know if any of these ASTM standards allow (or prohibit) the ‘yellow’ type of brass alloy?
Any alloy with less than 35% Cu is vulnerable. I don’t have all the ASTM call outs. Just check the stated alloy composition.
Regards